Tagged Under:
Discover the New and Improved Marching Hardware from Yamaha
An exclusive interview with the drums and percussion product marketing manager who provides insight into how the new line of carriers and stands were developed.
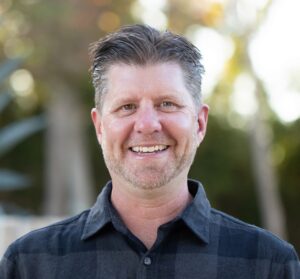
Joel Tetzlaff, Product Marketing Manager for the Yamaha drums and percussion department, discusses the exciting world of marching percussion as well as the cutting-edge Yamaha marching hardware products, scheduled to hit the market in early 2025 (they will be showcased at the 2024 Percussive Arts Society International Conference in Indianapolis). Tetzlaff unveiled the innovative design and manufacturing processes behind these game-changing products, revealing how they will elevate the experience for both marching performers and educators.
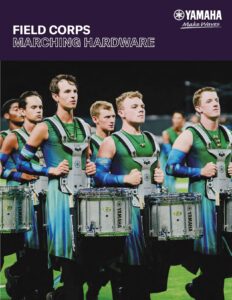
Download this Yamaha Field Corps Marching Hardware Brochure now!
Q. How does this new line of marching hardware from Yamaha differentiate itself from existing products in the market?
A. This new line of products will include both carriers and stands for marching snare drums, marching tenor drums and marching bass drums.
In this new line, we focused on developing hardware specifically for the marching arts. Marching hardware has evolved significantly over the years, and we aimed to take it a step further by focusing on simplicity and durability.
We gather continuous feedback from educators, and some of their suggestions have been incorporated into our new designs. For example, after hearing from band directors, we minimized the number of components on the hardware to ensure quick and efficient adjustments. We also focused on the reliability of these carriers and stands so that performers can focus more on music rather than worrying about the efficiency of the hardware.
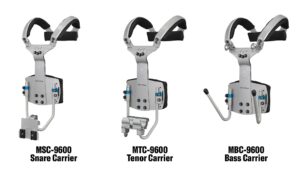
Q: Tell us about the MC-9600 Field Corps Carriers.
A: Our previous models of carriers did a good job of being dynamic with body styles and offering a range of adjustments. However, we recognized that too many adjustments can detract from the player experience, so, the MC-9600 Field Corps Carriers are both adjustable and comfortable. We reduced the number of components with only four player-side main adjustments, making set up a lot more straightforward and customizable. The flexible shoulders and wedge-shaped back bar provides confident movement.
THE YAMAHA EDUCATOR NEWSLETTER: Join to receive a round-up of our latest articles and programs!
We also reimagined the padding on our carriers. Understanding that they’re worn during long practices and performances, we developed a breathable fabric for the padding that dries quickly, enhances airflow, and resists moisture and odors, thanks to its plastic core. The padding is also removable and washable and features a C core inner padding that provides comfortable compression. This attention to detail ensures that we get our customers the best experience.
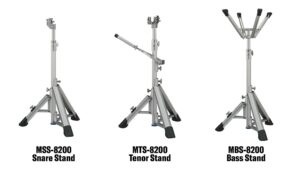
Q: Can you provide specifics about the MS-8200 Field Corps Marching Stands?
A; In developing these stands, we took shared elements from our drums department, but we didn’t just take the base of a drum stand and put marching configurations on top. We designed these stands specifically for the marching arts.
The hexrack core incorporates a slotted rail that perfectly balances lightweight construction with sturdiness, providing a stable foundation that’s easy to transport. The wide body legs and front leg adjustment are specifically sized to accommodate all terrains. And the twist-lock mounting system and height adjustment memory lock allows players to set their drum angles independently from the carriers, allowing them to “set and forget” their adjustments, which makes our stands ideal for marching.
We’re really proud of the seamless integration of our carriers and stands. Overall, we view these carriers and stands as integral to the instrument. Our carriers feature a more athletic approach while our stands provide a solid and lightweight foundation that meets the needs of modern marching performers. Rather than being another accessory, our new line of hardware products is designed to effortlessly integrate with the instrument itself.
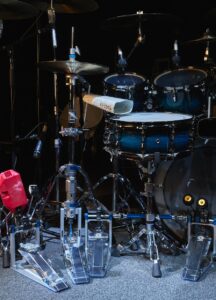
Q: How do these new products contribute to the company’s history of innovation?
A: We took a lot of shared knowledge we have between the different divisions of Yamaha, from racing to our music departments. What sets our company apart is our diverse manufacturing capabilities, specifically with metal. This allows us to create a shared database of our experiences, highlighting what has worked and what hasn’t.
For example, Yamaha Racing creates products designed for optimal performance in motorsports, reaching speeds of hundreds of miles per hour on a track. This brings up important considerations like the sturdiness and durability of materials, as well as their tensile strengths. I won’t dive too deep into the technical details, but this is what makes our manufacturing process truly incredible. We have resources at our fingertips, so we can ask questions like: “Do you think these two metals would work well together?” “Do these materials work well in this environment?”
This shared knowledge is what makes our hardware not just an accessory we import. Instead, all the products we design and build go through extensive research to help the make our instruments easier to use. As I mentioned before, this new line is built on the philosophy that our products are designed with a focus on simplicity and durability, which makes them reliable.
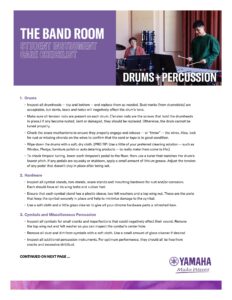
Download this Yamaha Drums and Percussion Care Checklist for Students now!
Q: Tell us about the extensive field research you did on these products.
A: Our new carriers and stands were taken out this summer for testing. Our first pretest was with Pulse Percussion, a Yamaha-sponsored indoor group. Our research was focused on adapting the carriers to various body types and determining how the carriers could be adjusted to comfortably accommodate a range of performers. After finding the middle ground, we took the carriers to the Cavaliers to be tested.
I accompanied our research and development team to visit the Cavaliers, and we focused on how these products would perform during the intense drum corps season. I believe that if a product can last through one drum corps season, it should hold up for five to seven years in a band room. The drum corps rehearse for six to eight hours a day in the heat and often perform that same evening, using the same products for both practices and shows. This intense schedule allowed us to put our new products to the test. We referred to this as our “Formula One test,” and I’m proud to say that we were very successful with the Cavaliers.
The performers reported that the carriers were comfortable, and they provided positive feedback throughout the season. Our team from Japan and I assisted with sizing the carriers, and we walked the Cavaliers through the different functions of the stands. We also checked up on them every two to three weeks, which helped me connect with many of the performers throughout the season.
According to the drum corps members, the standout feature was the padding. Some performers said it dried quickly during water breaks. Others were impressed that the carriers didn’t retain odors and provided enough comfort that they didn’t feel the metal. They also felt that the lightweight stands were easy to carry around their different stations.
Overall, our educators had a positive response to the tests as well. Many expressed relief and asked, “What took so long?” Educators said that the new carriers and stands were the finishing pieces to their Yamaha marching gear.
After testing, we identified a few areas for improvement — and we made about five to eight minor tweaks. None of these issues were major, but we felt that addressing them was crucial so we could get the best products out to our educators and performers. Part of our philosophy at Yamaha is that we don’t want to have one-time customers, we want to have them for a lifetime.
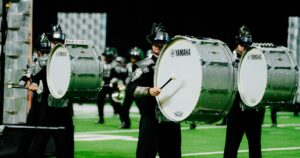
Q: What can educators do to ensure longevity and optimal performance?
A: Percussion is something that sits in the back of the room. What’s interesting is that the carriers or stands used by players is often specifically assigned to them for the season, but they don’t own them — unlike a saxophone that a musician uses to practice daily. So, it’s crucial for educators to instill a sense of ownership of these products in their students by emphasizing the idea: “This is my carrier. There are many like it, but this one is mine.” This helps students take responsibility for their equipment, ensuring that they report any loose parts or issues.
I always tell educators to conduct an inventory check at the end of each season. Maybe designate a responsible student or drum instructor to handle this task. It’s important to review the equipment and note any missing parts or issues that arose during the season. This way you can order any replacement parts ahead of time like lugs or bolts for the carrier, or wing nuts for the stands so the equipment is ready for summer. By taking inventory after each season, you can ensure that you are prepared for the next one. Also, if you anticipate needing new equipment or if you’re planning on adding a few more students to the roster, make sure to order it in advance.
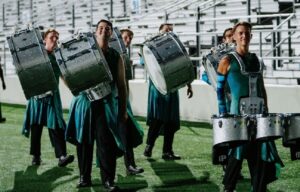
Q: How can this new line enhance student development, performance, practicality and comfort?
A: An important step in using the new carriers is ensuring that they are sized correctly for the performers. It’s crucial that the carriers are comfortable. Students and educators must keep in mind that when you first put on a carrier without a drum, it will feel different once the weight of the drum is added. So, make sure to revisit the sizing and make necessary adjustments after the drum is added. Don’t hesitate to adjust aspects like the belly plate height or the shoulder fit. These small tweaks can significantly enhance the performers’ experience.
It’s one thing to wear a carrier for a few minutes as opposed to hours. This summer, I observed the Cavaliers, and they were in their carriers most of the time. I believe the comfort of our carriers played a significant role in this.
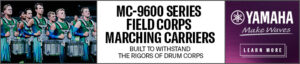
The new padding plays a key role in providing this comfort. As I said earlier, we really took a more athletic approach in developing this new line. Also, our new shoulder design securely locks the back bar in place, which allows movement to originate from the core, meaning that when the performer turns, the drum moves with them. Lastly, the simplicity of the products highlights a crucial aspect of supporting student development. With fewer moving parts, there’s less risk of things getting loose during rehearsals or performances. Once everything is tightened and locked in place, minimal maintenance is needed.
At the end of the day, it’s all about kids having fun while playing music. I get into the specifics of the gear because I love the gear, but the more time students can spend practicing, rehearsing and enjoying these products, the better it is for everyone.
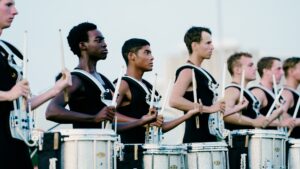
Q: What sets Yamaha marching products apart?
A: What sets Yamaha apart is how we create our products. When you choose a Yamaha, you can expect a level of consistency and quality that truly stands out.
There are other great options for hardware, but I think what makes our new products special is that they’re designed for exceptional durability, fit and finish. We’ve put a lot of thought into this new line of hardware, from the comfort and practicality of our carriers to how our stands are specifically built for the marching arts.
We believe in leading by example. Our focus is on creating high-quality products that elevate the experience of the performers and educators using our gear day in and day out.