Spotlight On Yamaha PHX Series Acoustic Drums
Creating the ultimate high-end drum kit.
What does it take to build the ultimate drums? That’s the question Yamaha designers asked in the early 2000s. Tapping into more than 40 years of drum building experience and input from world-renowned Yamaha artists, the quest to create the finest drums available led to the development of the Yamaha PHX (pronounced “Phoenix”) Series. Introduced in 2008, PHX are the company’s flagship drums, incorporating numerous innovations and combining the best of new technology with traditional craftsmanship to create the ultimate high-end drum kit.
Ready to learn more? Read on …
The Hybrid Shell
The heart and soul of every PHX drum is the shell, which features a unique 11- or 12-ply hybrid design combining several different species of tonewood.
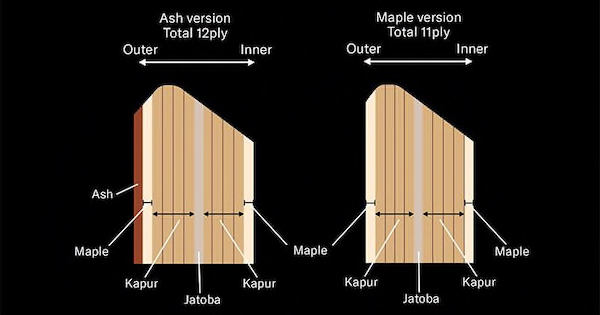
The center ply is Jatoba, an extremely hard and dense wood. This “core” ply is surrounded by layers of Kapur, which is in turn surrounded by layers of North American maple used for the interior and exterior plies. North American maple has traditionally been a popular choice for the construction of drum shells due to its hardness, but is actually the softest of the woods used in PHX shells. Constructing the shells with the hardest and most dense material at the core provides increased volume, a strong fundamental tone and a wide tuning and dynamic range. In following the company’s philosophy of “vertical integration” (where developments in flagship products are incorporated into other products down the line, wherever feasible), hybrid shell construction is also used in Yamaha Absolute Hybrid Maple and Live Custom Hybrid Oak Series drums.
As is the case with all Yamaha drum shells, PHX Series shells are hand-crafted using an “air seal” system whereby an air bag is dropped into the center of the shell mold and inflated, pushing outward against the interior ply and joining the plies together with uniform pressure throughout the shell. Diagonal, staggered seams and cross-laminated wood plies increase the strength of the shell and ensure that the shell holds its shape.
PHX drums are available in a variety of finishes (see the “A Wide Range of Choices” section below), with an exterior ply of either North American maple or textured Tamo ash. The ash veneer is less than half the thickness of a traditional coating so it doesn’t interfere with the resonance of the shell.
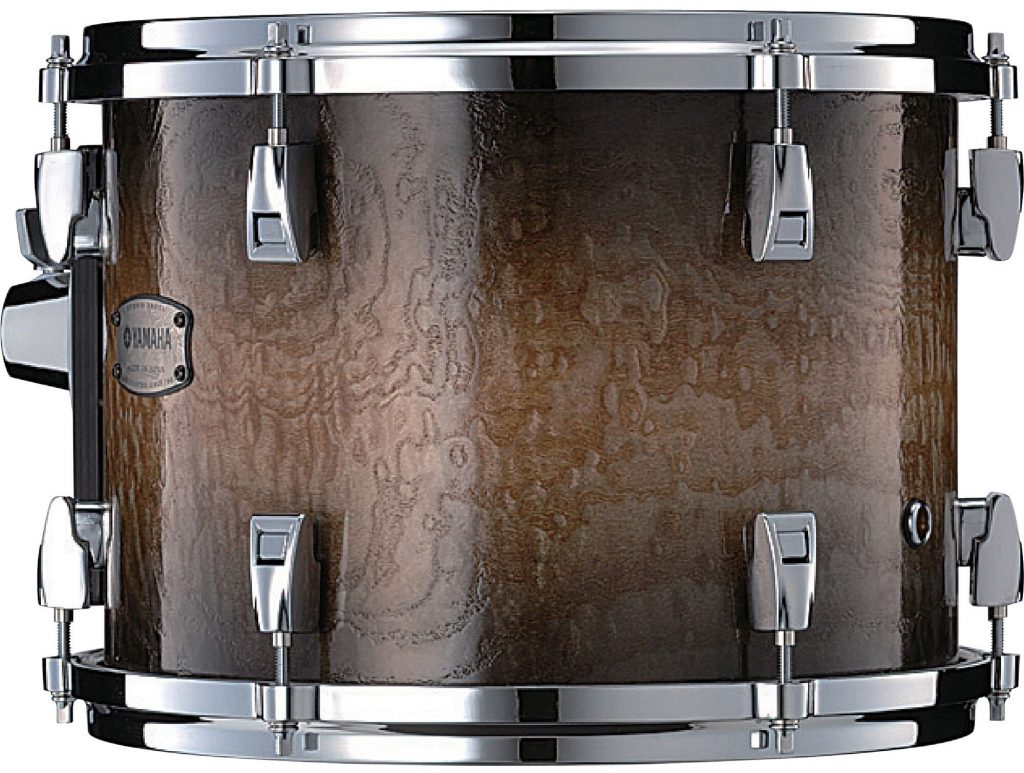
Bearing Edges
The bearing edge of a drum shell (the portion of the shell that contacts the drum head) has a huge impact on both tone and articulation. All PHX bearing edges are cut at 30 degrees and finished perfectly smooth by master craftsmen to guarantee easy tuning and a wide tuning range.
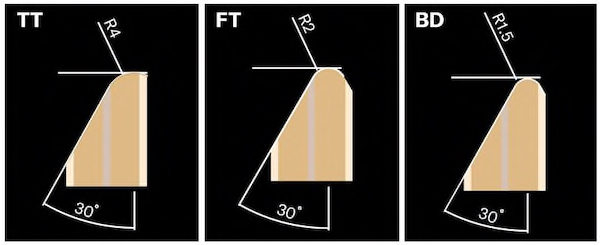
Y.E.S.S. (Yamaha Enhanced Sustain System) II Mounting System
PHX Series rack toms employ the Y.E.S.S. II shock mounting system, which permits the shell to vibrate freely while preventing unwanted movement. Incorporating a wood mounting plate (made from the same North American maple as the outer ply) and specially designed rubber inserts, the Y.E.S.S. mounts are located at nodal points on the shell — places where there is minimal vibration — to ensure that the mount does not interfere with the shell’s ability to resonate. The mounting points on larger toms are located where less desirable overtones are present, allowing optimum control over the decay and overtones produced by the shell. For drummers who prefer to mount their toms using stands, PHX bass drums are also available in an R-Version without the tom mount.
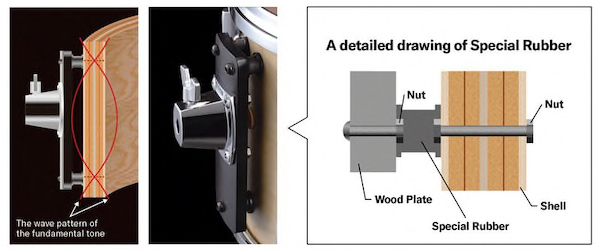
In another example of the aforementioned “vertical integration” approach, the Y.E.S.S. II mounting system is also used in Yamaha Live Custom Hybrid Oak and Absolute Hybrid Maple drums.
Hooked On You
The hook lug on PHX drums (as well as on Absolute Hybrid Maple drums) evolved from the Yamaha Nouveau lug, which was an innovation in lug technology. Designed to make head changes quick and easy, the hook lug has a small footprint and is located at a position on the shell where it mutes unwanted overtones and enhances the fundamental note. Its rectangular shape prevents rotation of the casing while tuning, guaranteeing that the tension rod is perfectly aligned, as well as providing firm support even when under high tension.
This kind of lug makes head changes much faster than with traditional lugs because the hoops can be removed simply by loosening the tension rods. Studio players will love the fact that they can convert their kit to concert toms in minutes without worry about rattling hardware, losing tension rods or washers, or the chance of cross-threading tension rods.
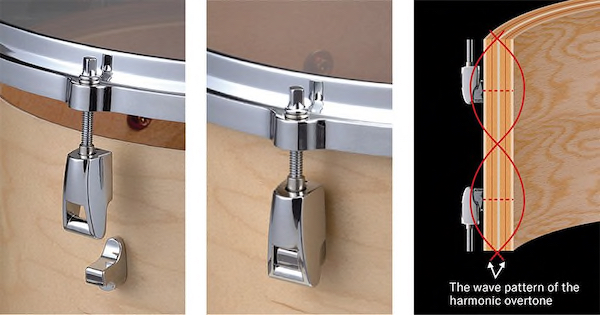
Attention To Detail
Every component used in the construction of a drum has an influence on the sound, including the hoops and the air vents. During the PHX R&D process, the Yamaha team discovered that die-cast hoops made from zinc can choke the sound of a drum — particularly smaller sizes such as 8-, 10-, and 12-inch toms. Die-cast hoops made from aluminum, however, provide rigidity, and deliver powerful rim shots and clarity of tone without choking the drum. That’s why PHX and Absolute Hybrid Maple drums utilize 3.0 mm die-cast aluminum hoops.
Vent holes allow air to escape from inside the shell, which improves the playing feel of the drum. They also affect the pitch, projection and decay of the drum. Depending upon the dimensions of the shell, PHX drums have between one and ten air vent holes. As the size of the drum increases, so does the number of air vents. A large PHX floor tom can have six vents while a bass drum may have eight or ten, depending upon the size.
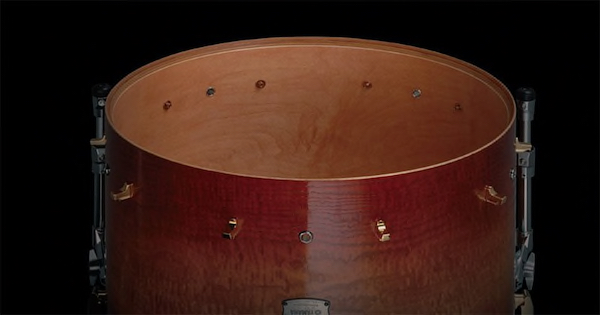
Increasing the number of air vents lowers the fundamental pitch and shortens the decay. All of these variables have been fine-tuned in PHX drums to create the optimum tonal balance and playing experience.
A Wide Range of Options
PHX Series drums are meticulously hand-finished in a variety of eye-catching colors and high-quality finishes, accentuated with gold or chrome hardware. Maple PHX drums are available in either matte or gloss finishes, while the Ash models are available in gloss or textured finishes (the latter has a slight shine to it).
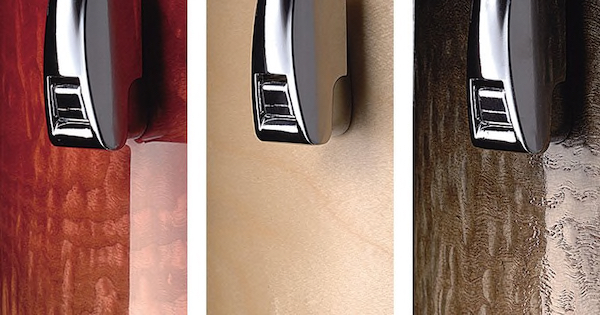
These finishes have been rigorously tested for resistance against changes in humidity or fading from exposure to UV light, guaranteeing that they will sound and look beautiful for a lifetime.
Here are some videos that show how PHX Series drums are constructed:
Check out this video of Yamaha Artist Larnell Lewis playing the PHX: